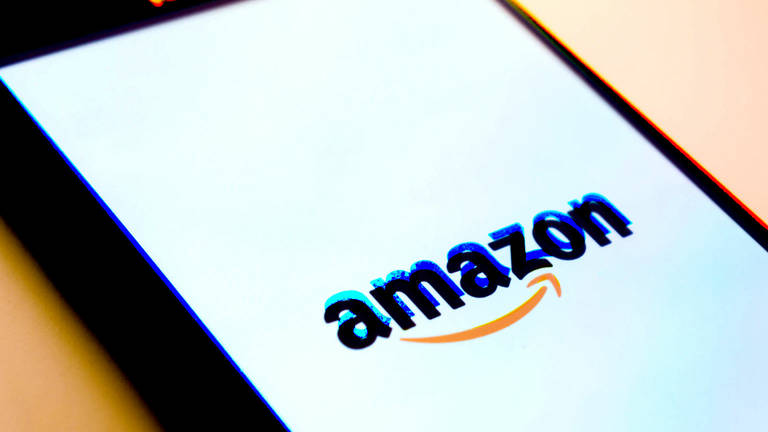
About 13 million users click the order button on amazon.com every day. A few days later, all or at least almost all of the 13 million orders are delivered at their destination. But what happens in between?
How does Amazon gets to deliver the package to you?
Well it depends... a lot. In fact, Amazon's delivery system (transportation system) is more complex than almost any logistics company. It's much more complicated than UPS, FedEx, DHL, or any other major delivery company.
Counterintuitively, this complex fulfillment system is a key part of Amazon's secret to success. They strive to simplify the customer experience through complexity behind the scenes. Back to the question: How does the Amazon package get to you? The answer depends on several factors.
Amazon has nothing to do with fulfilling these orders, and the process looks like the same as any other e-commerce business. The difference is how the other three quarters of Amazon packages get to you in the United States, those packages that are fulfilled directly by Amazon.
Their approach initially depends on the size of the package. Amazon fulfillment centers are more or less divided into three categories: Small Sortable products, Large Sortable Products, and Large Non-sortable Products.
The next category, large sortable, is basically everything bigger than that of the previous category, with the maximum of about 27kg.
The reason for the separation of large and small items is that the processing of small items is easier to automate - they can be installed on conveyor belts, automated robots and other tools that reduce the company's dependence on humans.
For example, Amazon uses a robot called "Amazon Kiva", which is fundamentally changing the way the company's order pickers operate, and the way staff find items in the warehouse.
Using these robots, a person can pick up three to four hundred items per hour, instead of the hundred that can be picked up on foot. Of course, given that Amazon has come under a lot of criticism for its treatment of workers, and because people are very expensive even with low wages, Amazon also benefits from the reduced number of people involved in the process.
In most cases (but not all), fulfillment centers for large and small items are located under one roof, although they operate completely independent of each other. Of course, for Amazon, the ideal solution is to store every item in every warehouse, but that's not realistic. Therefore, they use predictive models to try to place the items closest to the customers who are most likely to buy them.
For example, Miami residents may not want to buy a lot of ice scrapers for their cars, while in Fargo, North Dakota, demand for this product is almost certainly high. So it's no surprise that when you look at the data, the colder the city, the faster you can get ice scrapers on Amazon. That's Amazon’s predictive stocking at work.
While most of the system's examples are more nuanced and unintuitive, the concept is simple: its algorithm brings the product closer to the consumers who are most likely to buy. It is possible using modern big data analysis, available only at this scale.
These facilities are less automated than sortable facilities and even include staff creating custom boxes for odd items. For example, in Colorado, this is a completely independent facility in Aurora, separate from the sortable fulfillment center in Thornton.
Some large items are transferred directly to a third party provider, typically XPO Logistics, which transports those large items to the final destination, while other items continue to run on Amazon's system. The portion of large non-sortable items that have not been sent to the external logistics provider, as well as all small and large parcels, will be sent to the regional sorting center.
In Colorado, those two fulfillment centers send packages to a single sorting center just minutes from the Aurora fulfillment center. It is a huge facility with an area of almost 500,000 square feet. The robots run and throw packages at different chutes, each chute representing a different zip code group.
Amazon has managed to use 21st century technology and techniques to build a 21st century logistics network. Of course, part of the threat comes from the dominance of the company. Today, the way FedEx and UPS deliver packages is basically the same as it was decades ago, but Amazon's system become possible only through innovations that allow them to manage such a large, complex, and convoluted system.
If you are concerned about Amazon's growing status as a global one-stop-shop, rest assured because they will only get better. More importantly, the rise of Amazon proves that the internet is the major new main street, whether we like it or not.