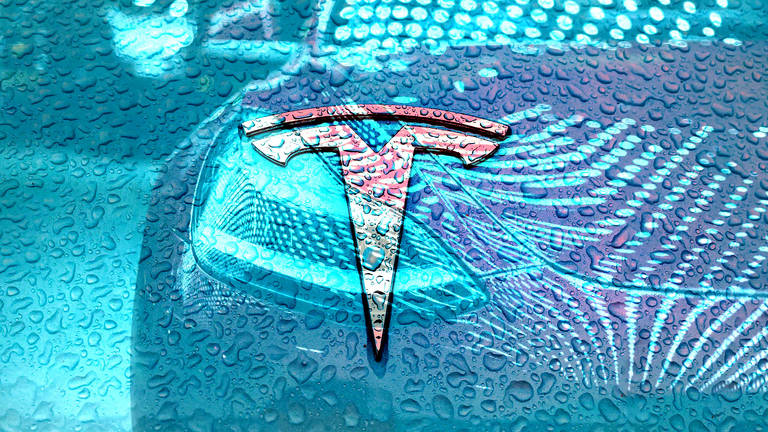
Tesla's gigantic gigantic factory in Sparks, Nevada, has for some time now been able to produce battery packs for the company's groundbreaking series of electric vehicles at a rate of around 5,000 per week, in terms of volume, which puts Elon Musk's operations in a stronger position than all other competing electric car companies combined.This is a major contributor to the company's soaring share price, which lets Elon Musk have the world's highest bank balance.
Elon Musk made no secret of the fact that one of the biggest stumbling blocks he faces on his path to weaning mankind off the internal combustion engine is the quality and capacity of the batteries his cars use. Making a car run on electricity is apparently simple enough, but storing enough precious juice on board to make electric car ownership a comparable, or even superior proposition than normal gas guzzlers has thus far proven elusive.
While other aspects of technology, particularly microchips and integrated circuits, have become exponentially more powerful and compact over time, Battery technology has lagged behind, both in terms of technical sophistication and in terms of the ability to quickly and easily deliver and manufacture units on a large scale.
For now, and at least over the next few years to come, Tesla is working in partnership with Japanese electronics company, Panasonic, an old hand in the battery business, but instead of offering a way to have batteries made at a Panasonic factory, Elon Musk cleverly insisted that Panasonic brings its production lines to the Tesla gigafactory.
The benefit of this, of course, is that it avoids stubborn shipping delays, but also thanks to the considerable resources Elon musk owns, the battery design process can literally use the largest building on planet Earth.
Cell aging is an integral part of the battery cell manufacturing process. When a cell first leaves the assembly line, it is completely useless (from a chemical point of view) until a protective layer called the solid-state electrolyte interface forms around the electrodes. This can take 10 to 12 days, although innovations in the gigafactory have allowed Panasonic engineers to age cells in place as part of a whole battery rather than individually, which is far more efficient and therefore faster.
It should be emphasized at this stage that Elon musk factories are not simply warehouses that just happen to be crammed with buzzing machines. In his opinion, how they operate and function is just as important as the finished car itself.
Elon Musk said at a general meeting, a few years ago: We realized that the real problem, where the greatest potential lies, is building the machine that makes the machine. In other words, building the factory. I really think the factory is like a product."
Therefore almost no detail is left a chance. The gigafactory itself, for example, was not just plonked down at random on a conveniently flat piece of desert by accident, but instead the entire vast 15 million square feet facility lies on a strictly precise north-south axis.
This is partly to get the most out of the solar panels on the roof, but it also helps to optimize the sophisticated indoor navigation systems for the factory's small army of robots.
These robots perform much of the car and battery-related manufacturing tasks in the factory. For example, when components need moving from inventory to the production line, robots perform the function faster and more reliably than humans using a combination of smart GPS devices and magnets embedded in the floor. This is also a blessing from an occupational safety point of view. However, this does not mean that every detail of operations in the Gigafactory is automated, but reflects Elon Musk's data-led approach.
When a job is demonstrably tackled better by human beings, for instance connecting lengths of dangling pipe a human being is duly hired as musk himself admitted not long ago: "we went too far in the field of automation and automated some pretty silly things."
Panasonic's expertise is indeed a key factor in Tesla's success. At the very least, the electronics giant is said to have put around $1.6 billion into its work at the Gigafactory, not least to add a 14th production line to the gigafactory last year to meet demand. In fact, the company is only now starting make a meaningful return on its investment.
Even so, Panasonic knows just like anyone else that Elon Musk is not a man who tolerates less than exemplary performance, and as it happens, Elon has been extremely vocal about its desire to make its own batteries as soon as it is commercially feasible. Although back in June, Tesla and Panasonic renewed their commitment to work together until 2023 elon musk is openly hiring engineers to start building in-house batteries at Fremont, California and at the forthcoming Gigafactory in Berlin.
He inspired Panasonic to come up with new, more efficient and faster techniques for delivering the latest generation of 2170 lithium-ion cells currently being used in the Tesla model Y. With denser, more efficient batteries like these which largely supersede the older 18650 batteries Tesla previously used is key to Tesla's vision of making electric cars even more efficient quicker out of the factory and crucially more affordable over the coming years.
Elon Musk's very ambitious public demands, like his promise to deliver a Tesla with a ticket price of 25,000 in the next couple of years certainly serves to keep Panasonic's widths sharp and their production methods lean as ever a man with his eye on the horizon.